Our goal is to overcome the challenges of integrating many different devices and data sources into a single, easy-to-use IoT data platform. With our solution, which is largely based on well-established and secure open source software, you can store, visualize and transform data and information and create tailor-made applications - without being tied to a vendor and as a long-term investment for your future IoT strategy .
For one of our customers we developed a turnkey solution to continuously transfer 3000 data points from 15 OPC-DA and UA servers to an IoT database. Our customer managed to visualize and analyze the data within 6 weeks - an effort of 21 man-days.
SWMS Project Manager tweet
Challenge
The customer operates a complex facility for sorting and processing large volumes of packaging waste that is delivered from Germany and the Netherlands. The plant consists of various components such as mechanical separators, magnetic separators and air classifiers. So-called near-infrared sorters, which separate the packaging waste into two fractions, play a special role in sorting. More than twenty of these NIRs are installed in the plant. The system's SCADA data comes together in the shift manager's office, from which the system is controlled and the current status of all sensors, drives and aggregates can be monitored and adjusted. What the customer has been missing so far is the online availability of the data and the possibility of persistent storage of the IIoT data in order to have it permanently available. This is a requirement for generating periodic reports on plant operations, leveraging the data in third-party systems, and developing data analytics applications to optimize plant operations.
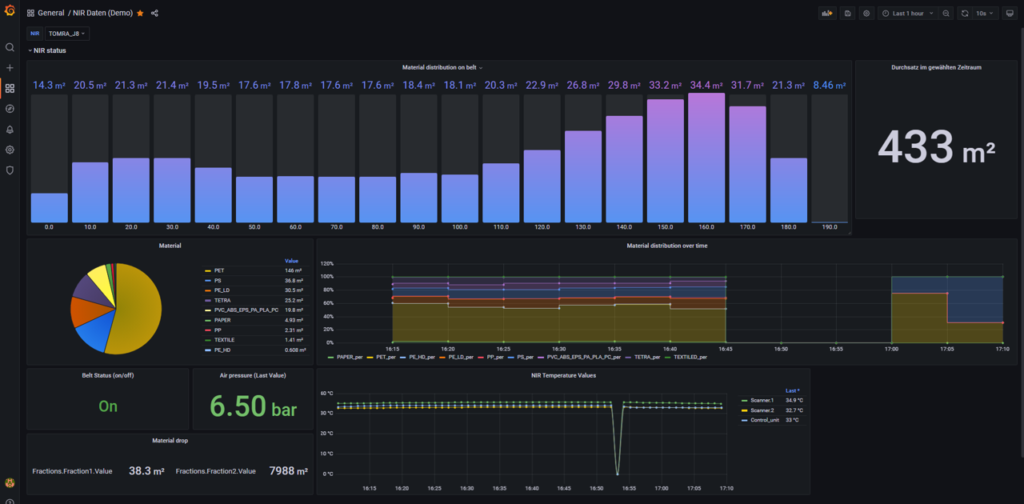
Proceedure
The implementation of the individual IoT platform for the customer was divided into five work packages.
1. First, an extensive architecture workshop was conducted on-site at the factory, during which SWMS understood the customer's process in detail and analyzed the customer's requirements. Various system architecture options were presented and discussed. As a result, the customer was presented with an architectural concept for data acquisition, transmission and storage.
2. In the workshop it was determined that the system should use both OPC UA and OPC DA servers as data sources. Based on this, the gateway was configured according to customer requirements. The continuous polling of more than 3000 data points has been configured. In addition to querying, pre-processing and buffering the data, the gateway controls the forwarding of the data via the IIoT standard protocol MQTT.
3. In the cloud, SWMS set up various open source services in the customer's data center, with which the data is first pre-processed and then persisted in a high-performance time series database Influx DB. In addition, a Grafana instance was set up to create dashboards.
4. After the components had been set up successfully, the gateway was commissioned and connected on site in just under two days. All functions were tested and the system was finally configured.
5. In the last work package, the customer's employees were trained so that they can independently make changes to the gateway and create their own dashboards.
Result
With an effort of about 21 consultant days, the work packages 1-5 and thus the project were successfully completed. The customer now has a growing database that is used directly for weekly/monthly evaluations and for live dashboards on system operation and enables faster reaction to downtimes and errors. In addition, the basis for further evaluations of the data is created, with which optimization potential can be identified in the future.