Project example data analytics
"The acquisition of operational data (BDE) represents the basis for increasing potential in production. The system for operational data acquisition and order management developed together with the customer enables increased transparency and well-founded decisions regarding product and process."
SWMS project manager
Challenge
Due to individual and complex processes for manufacturing products, the use of both standard solutions and individual developments is often not suitable for small to medium-sized companies in the production environment - the actual step towards Industry 4.0 is therefore often difficult. The effort for the development of an individual solution or for the extensive adaptation of standard software is too great. For this reason, many central production processes, which represent a not inconsiderable part of entrepreneurial know-how, are not supported by IT systems today. In many cases, these processes run manually, accompanied by paper-based documents or simple Excel files.
As already described in this project example, we identified such manual processes at one of our customers and, together with the customer, determined that the basis for increasing potential in production is the collection of operating data (BDE). Their evaluation promises the necessary instrument for well-founded decisions regarding the product and process in the short, medium and long-term planning phase. In addition, the focus is on increased transparency towards customers.
The aim of this project was to develop a system that replaces the manual control of orders with production based on paper-based order documents and via which the relevant information about the orders can be recorded - the app basis for Industry 4.0, so to speak.
Proceedure
Based on the user and process requirements, the system for production data acquisition and order management was specified and, based on the EPC Information Services (EPCIS) standard, an event model was developed in order to be able to flexibly record various events in the production process via the BDE. This includes the generation of order-related events at the workstations for incoming and outgoing orders and captures the following information
- ID for unique identification of the event
- Reference to the component, batch or order
- Process step that describes the activity carried out for the event
- Location in production or planning
- Timestamp of the event
- Event info for securing process-relevant information (e.g. quality checks)
The Microsoft Power Platform was used to develop the application and thus a so-called low-code approach was used. This enables the creation of individual applications in a fraction (estimated 10%) of the development time that would be necessary for the development of a native app, provided that the chosen platform fits the task and the requirements.
Essentially, the architecture of the application consists of three components:
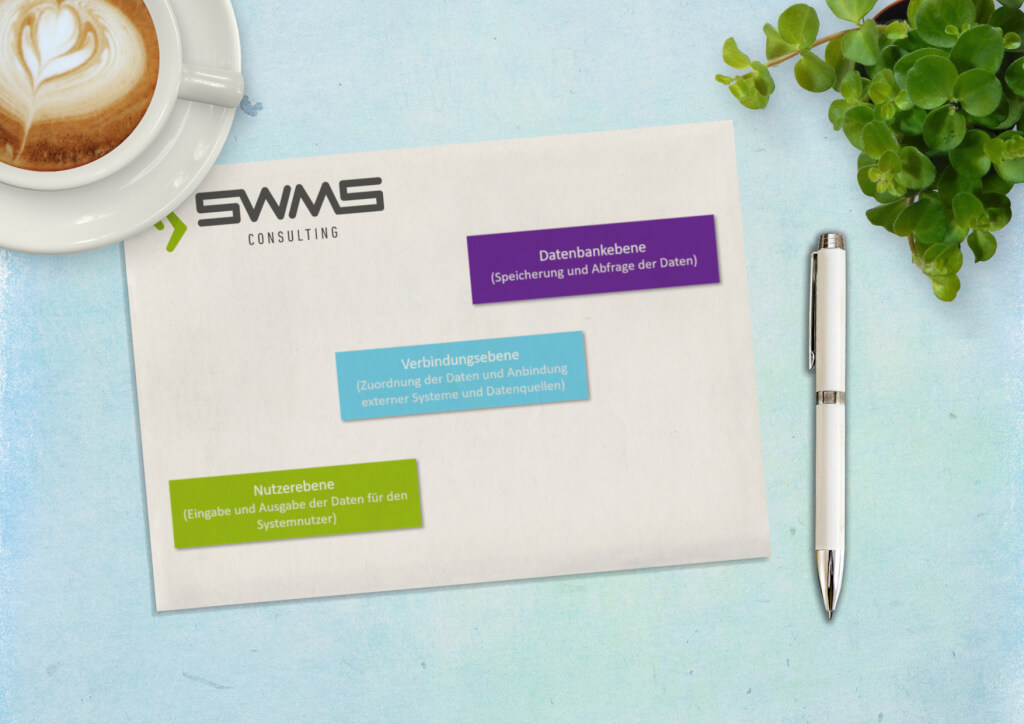
user level: Interface on which all data entry and tasks in planning and production are carried out. The Microsoft PowerApps tool was used here. The user interface is created using a graphical editor and the desired functionality is created with the help of functions.
database level: The noSQL database, which is provided on the Microsoft Azure cloud platform, was chosen to store the events. Complex queries can be implemented on the database using scripts.
connection level: The automation tool Microsoft PowerAutomate was used to transfer the data between the user interface and the database. In addition, this tool enables the connection and automated use of other services, such as sending emails and messages, connecting ERP systems and other data sources, connecting systems for data analysis and developing your own connectors. This means that in the future it will be possible to use this connection level for the development and integration of further systems. The individual functions are put together using so-called flows, which are configured using a graphical user interface.
The project was implemented in close cooperation and iteratively between the customer and SWMS. Within a few days, a first system draft was presented to the customer, which was then gradually further developed on the basis of feedback from the operationally responsible process participants.
Result
In this project, an individual system was developed for the customer that directly affects two roles in the company.
1. The production planner is supported in planning and monitoring production orders. For this purpose, options for importing customer orders from the ERP system and creating warehouse orders were developed. The orders can be monitored via an order overview and managed and released from a central location. The production planner is also able to process the orders and call up important information about the production process via order research.
The following screenshot shows a screen for creating warehouse orders:
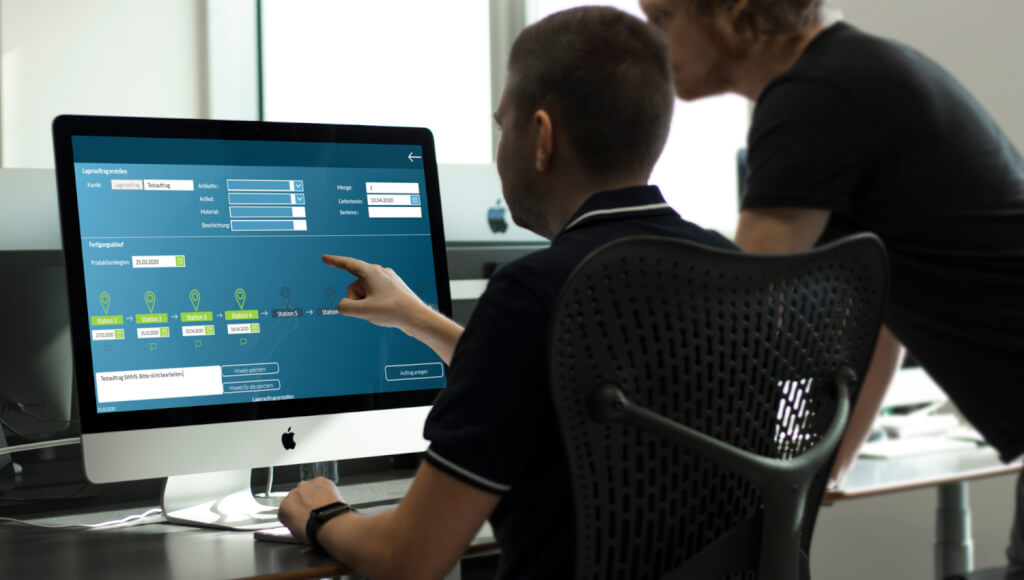
It is interesting here that an individual production process can be created for an order depending on the product, material availability and capacity utilization of the workstations. On the basis of information from merchandise management and the findings of the recorded data, there is potential at this point to display further information and assistance for the planner.
2. The employees at the workstations were equipped with a tablet that replaced the paper-based order lists. Depending on the workstation, the employee has access to the information relevant to him. The following screenshot shows an order overview screen:
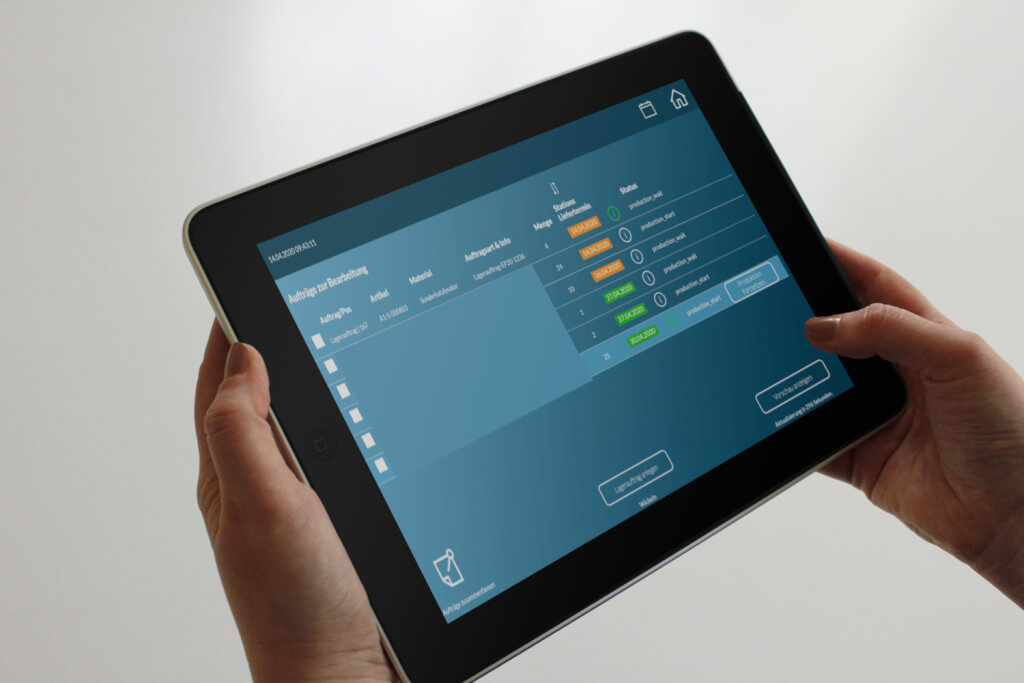
The information presented is used for order processing. In addition, the employee can produce partial or excess quantities and create error messages via the system. As part of the processing, the events described above are recorded and stored and are therefore available for evaluation purposes.
The following effects have already set in for the customer (excerpt):
- Time savings in planning, avoidance of many walking routes for the production planner
- Increasing the quality of processing orders
- Greater transparency in production, as the order status can be tracked
- Monitoring of compliance with (station) delivery dates
- Simplified communication between planning and production
- First evaluation options for the process planner
The following effects for the customer are expected in the future from the created basis (excerpt):
- Further time savings in the planning and production process
- Increasing the quality and verifiability of quality indicators
- Development of a key figure system based on the collected data
- Improving internal communication channels, also by involving other departments in the company
- Use of the created database for further evaluations and the return of the results in the production planning processes (detailed planning)
- Semi-automatic production planning and control based on lot size optimization at the workstations
In the project, a system was developed in a very short period of time (20 consulting days for potential analysis, implementation, testing and IT security check), which is used operationally in production and which offers starting points for further digitization projects. In addition, the system can be adapted relatively easily to changes in the process and the customer can train their own key users, who can make adjustments to the system independently in the future.
This project was funded by the go-digital funding program of the BMWI.
